Time cut from several weeks to a few hours using Stratasys Production 3D Printer
GKN Aerospace is producing complex tools that were uneconomical or impossible to make without additive manufacturing
MINNEAPOLIS & REHOVOT, Israel — (BUSINESS WIRE) — September 5, 2018 — Stratasys (Nasdaq: SSYS) today announced that GKN Aerospace is improving production times and removing design constraints for multiple tooling applications since integrating additive manufacturing at its Filton manufacturing site in the UK.
This press release features multimedia. View the full release here: https://www.businesswire.com/news/home/20180905005501/en/
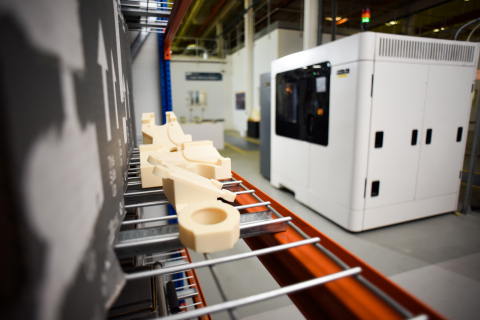
3D printed tooling produced on the Stratasys F900 Production 3D Printer (Photo: Business Wire)
GKN serves over 90 percent of the world’s aircraft and engine manufacturers with aerostructures, engine systems and technologies.
According to Tim Hope, Additive Manufacturing Center Manager, at GKN Aerospace, the company decided to invest in the Stratasys F900 Production 3D Printer in a bid to cut lead times for production-line tools, and to create complex parts, impossible to make with traditional manufacturing methods.
“Since integrating the F900, we have dramatically reduced production-line downtime for certain teams and are enjoying a new found freedom to design complex tools,” he says.
Traditionally, the lead-time required to produce a metal or plastic replacement tool is several weeks. Now, with the ability to use an in-house production 3D printer to do the same job, the replacement burden has been removed and the responsiveness to manufacturing requirements improved.
“We can now cost-effectively produce tools for our operators within three hours,” Hope explains. “This saves critical production time, and by printing in engineering-grade thermoplastics, we can produce 3D printed tools with repeatable, predictable quality every time. All while matching the quality of a traditionally-produced tool, and reducing the costs and concessions compared to equivalent metallic tooling.”
While GKN Aerospace is using a standard thermoplastic today, it is experimenting with Stratasys’ high-strength, heat-resistant ULTEM™ 1010 Resin material for these applications.
Customized, complex tools that were previously impossible to make
In addition, GKN Aerospace is reporting unprecedented levels of design freedom since investing in the Stratasys F900 into its operations.
“One of the key benefits of additive manufacturing is the creative freedom this technology affords users,” explains Hope. “The F900 offers the largest build-size of any FDM 3D printer enabling us to rapidly produce tools to meet any requirements. Most notably, complex geometries and cavities that would otherwise be problematic are now practical with the F900. We’re utilising it to design, and 3D print, previously inconceivable tools that enable us to manufacture complex parts that are uneconomical or just physically impossible by other methods.”
In addition to design freedom benefits, GKN Aerospace has also seen a 40 percent decrease in material waste.
To the future
Hope anticipates a greater move towards the use of FDM additive manufacturing to produce high-value, flight-critical, end-use composite parts.
He says. “GKN Aerospace’s product range is vast, and we see large-scale FDM and carbon-reinforced parts as the future of additive manufacturing in aerospace. By using Stratasys additive manufacturing for tooling, we are harnessing a machine that offers us the freedom to produce unique and complex tools of any size, with the build quality to match any manufacturing requirement. All while simultaneously preparing ourselves for the future.”
Stratasys is a global leader in additive manufacturing or 3D printing technology and is the manufacturer of FDM® and PolyJet™ 3D Printers. The company’s technologies are used to create prototypes, manufacturing tools, and production parts for industries, including aerospace, automotive, healthcare, consumer products and education. For 30 years, Stratasys products have helped manufacturers reduce product-development time, cost, and time-to-market, as well as reduce or eliminate tooling costs and improve product quality. The Stratasys 3D printing ecosystem of solutions and expertise includes: 3D printers, materials, software, expert services, and on-demand parts production. Online at: www.stratasys.com, http://blog.stratasys.com and LinkedIn.
Stratasys, FDM, and Fortus are registered trademarks, and the Stratasys signet is a trademark of Stratasys Ltd. and/or its subsidiaries or affiliates. ULTEM 1010 Resin is a registered trademark of SABIC or its affiliates or subsidiaries. All other trademarks are the property of their respective owners.
Attention Editors, if you publish reader-contact information, please use:
- USA 1-877-489-9449
- Europe/Middle East/Africa +49-7229-7772-0
- Asia Pacific +852 3944-8888
View source version on businesswire.com: https://www.businesswire.com/news/home/20180905005501/en/
Contact:
Stratasys Media Contacts
Stratasys Corporate & North
America
Email Contact
+1
518 424 2497
or
Email Contact
+1
952 906 2726
or
Europe, Middle East, and Africa
Jonathan
Wake / Miguel Afonso
Incus Media
Email Contact
+44
1737 215200
or
Greater China, Southeast Asia, ANZ, and India
Email Contact
+
86-21-33196051
or
Japan and Korea
Email Contact
+81
3 5542 0042
or
Mexico, Central America, Caribe and South
America
Email Contact
+52
55 4169 4181
or
Brazil
Email Contact
or
Email Contact
GP
Communications
+55 (11) 3129 5158