2021 1.0.1 Enables Collaborative BIM and CAD Workflows, New Functionalities for Metal 3D Printing and Sheet-Metal Manufacturing, and more
BROOMFIELD, Colo. — (BUSINESS WIRE) — May 13, 2021 — Spatial Corp, the leading provider of 3D software development toolkits for design, manufacturing, and engineering solutions, and a subsidiary of Dassault Systèmes, announces today the production release of 2021 1.0.1. This release delivers new advances in enabling architectural and engineering workflow crossover for BIM workflows; automated support-creation suitable for metal 3D printing; fast sheet-metal manufacturing; hard edge detection in polyhedral models; and entity comparison and multi-threaded canonic simplification as well as higher order canonic-to-lower-order canonic conversion support for 3D ACIS Modeler.
This press release features multimedia. View the full release here: https://www.businesswire.com/news/home/20210513005870/en/
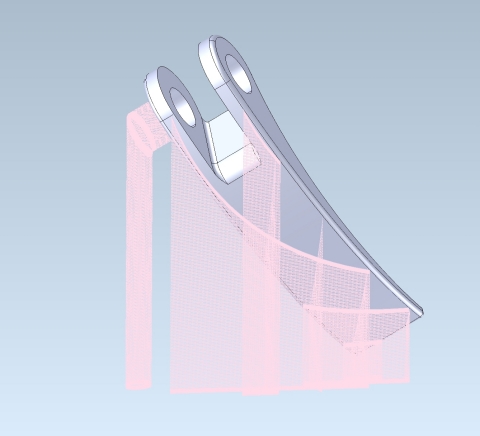
Supports created by CGM Modeler for a lightweighted lever. The lever is ready for 3D printing. (Photo: Business Wire)
On-going advances in software permit increasing integration of architectural and engineering workflows to extend the traditional functionality of BIM applications. As a result, architects and engineers can more easily collaborate virtually to optimize both architectural form and engineering function —while changes are still easy and before any expensive procurement and construction begins.
New in 2021 1.0.1, 3D InterOp introduces the filtering of classes in IFC files. As a result, 3D InterOp can be directed to import specific data in an IFC model (for example, architectural elements from specific IFC structural classes in tandem with mechanical or electrical components in other IFC classes). 3D InterOp’s ability to filter various classes in IFC files allows users of BIM applications (built upon 3D InterOp) more flexibility to focus only the design-relevant parts of large complex architectural models for downstream workflows.
3D Precise Mesh allows the creation of boundary-layer meshes, which are important for computational fluid-dynamics (CFD) analyses in which regions of high-speed flow are present. High-speed flow examples include water-flow along ships’ hulls, airflow around an aircraft wing and airflow near duct outlets for an HVAC system in a building. In such cases, the accuracy of CFD analyses is improved by adding boundary-layer meshes to simulation models.
Spatial’s 3D InterOp and 3D Precise Mesh components enable multi-role teams of architects, interior designers, supply-chain purchasers, engineers and technicians to collaboratively work together and conduct “trial and error” tests of designs – all virtually, when design changes are relatively easy, thereby saving project time and ultimately costs.
For specific details about these features, as well as an example workflow featuring these new functionalities, please see Spatial.com.
Accelerate 3D Printing: Automated Lightweighting and Support-Creation with CGM Modeler
With the release of 2021 1.0.1, CGM Modeler introduces a series of new operators for the creation of supports in Metal 3D printing applications. These new operators allow quick creation of supports with perforation patterns, anchors to parts and printing trays, and both simple and knee supports for hard-to-reach geometric features (e.g., recessed holes). These supports are especially suitable for additive processes that take place at high temperatures, such as powder-bed fusion or material extrusion, as the resulting perforated support and anchor structures (e.g., teeth) are very good at dissipating heat. Furthermore, the perforations make the anchors easy to remove for post-processing (i.e., deburring and finishing).
Digital design allows engineers to optimize virtual parts for not only in-service performance — weight, reliability, appearance — but also manufacturability and ultimately cost. Parts intended for 3D printing offer new design opportunities previously unobtainable by traditional subtractive manufacturing methods and are particularly ideal for virtual optimization.
With functionality embedded in CGM Modeler, developers can quickly write user-friendly 3D printing applications that quickly eliminate unnecessary material yet still maintain necessary stiffness by hollowing solid volumes and adding stress-bearing patterns such as ribs, buttresses and even complex lattices.
For specific details about the new features in CGM Modeler, as well as an example workflow featuring these new functionalities, please visit Spatial.com.
Fast Sheet-Metal Manufacturing: Quickly Detect Bends and Unfold Parts with CGM Modeler
In 2021 1.0.1, CGM Modeler introduces a new operator to automatically detect both cylindrical and conical bends in 3D boundary-representation (BREP) models. As a result and when combined with existing operators in CGM Modeler, software-developers can enable even more automation in sheet-metal manufacturing applications.
Often sheet-metal is the obvious choice for a myriad of industrial uses ranging from brackets and enclosures to ducting and car bodies. An important element of sheet-metal design is the ability to virtually reverse the manufacturing process to unfold CAD parts and lay the original sheet-metal flat. Then, features can be removed and the exact size of the sheet-metal blank can be determined and optimally nested within standard sheets for automatic cutting.
The entire workflow for the detection of bends and virtual unbending and defeaturing of sheet-metal parts can be implemented into any CAD-CAM software-application with Spatial’s powerful CGM Modeler.
For specific details about the new features in CGM Modeler, as well as an example workflow featuring these new functionalities, please visit Spatial.com.
Find Your Way Around Tessellated Geometry: Spatial Now Supports Canonic Edge and Face Recognition in Polyhedral Models
With the 2021 1.0.1 release, CGM Polyhedra introduces “segmentation” to detect canonical edges and faces in polygonal models with only tessellated geometry.
Traditional boundary-representation (BREP) models for CAD geometry are ubiquitous throughout the CAD industry and are noted for their preciseness. However, sometimes such preciseness is not needed and instead speed is preferred. This is especially true for large models comprised of many separate parts. Furthermore, oftetimes BREP geometry is not even available – especially in downstream workflows. Instead, only tessellated geometry (e.g., STL files) is available.
Because polygonal models lack the preciseness of solid BREP models, one historic drawback of polygonal models has been inability to robustly detect features such as canonical edges and faces in tessellated geometry. Canonical edges and faces often define important entities like holes, pockets, bosses and bends, which must be identified by CAD/CAM applications for additional processing.
Spatial’s CGM Polyhedra polygonal modeling engine now has the answer. CGM Polyhedra now provides a “segmentation” operator that allows applications to robustly detect canonical edges and faces in tessellated models. As a result, application developers can implement detection of high-order features such as holes, pockets and bosses in their applications.
For specific details about the new features for CGM Polyhedra, as well as an example workflow featuring these new functionalities, visit Spatial.com.
Enable CAD Workflows in Parallel: Quickly Reconcile Multiple Design Changes to the Same Model with Entity Comparison in the 3D ACIS Modeler
In 2021 1.0.1, 3D ACIS Modeler introduces “entity comparison” to identify overlapping versions of the same model. Such cases sometimes arise, when slightly different versions of the same model exist.
Complex virtual engineering projects often require technical drafters and engineers to work collaboratively across multiple departments and time-zones. As such, modern CAD applications typically allow parallel workflows. However, sometimes a multitude of designers working on different aspects of a project – say a car-body – causes problems.
For example, two drafters working on the same CAD model at different times can create overlapping versions of the same body. As a result, it can be rather difficult to reconcile design changes made by different drafters to the same model.
Spatial’s 3D ACIS Modeler now offers new functionality to mitigate the effects of changes to the same model. More specifically the 3D ACIS Modeler offers “entity comparison”, whereby different changes to the same body in a model can be automatically visualized and quickly reconciled. This allows developers to reduce their application’s dependency on a series of Boolean operations to compute such comparisons.