New research studies verify the biomechanical accuracy of 3D-printed orthopedic models
EDEN PRAIRIE, Minn. & REHOVOT, Israel — (BUSINESS WIRE) — December 2, 2020 — 3D printing leader Stratasys Ltd. (NASDAQ: SSYS) has enhanced its J750 Digital Anatomy™ 3D printer with advanced bone capabilities that don’t just look real but are actually biomechanically realistic, backed by clinical research. The software upgrade enables the systems to mimic porous bone structures, fibrotic tissue, and ligaments so medical professionals can create models that behave just like human bone.
This press release features multimedia. View the full release here: https://www.businesswire.com/news/home/20201202005096/en/
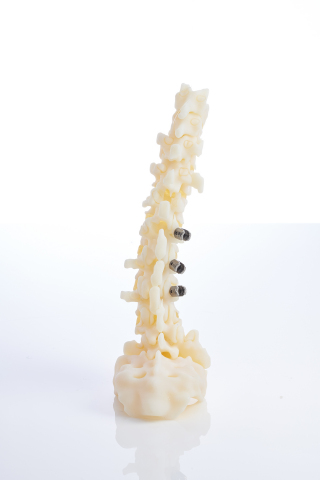
The Digital Anatomy 3D printer from Stratasys enables physicians to practice inserting screws for orthopedic applications with biomechanical realism similar to a human anatomy. (Photo: Business Wire)
The Digital Anatomy printer was first introduced a year ago, with an initial focus on mimicking soft cardiology tissues, such as hearts and blood vessels, using powerful Digital Anatomy software and materials like GelMatrix™ and TissueMatrix™. The technology has helped healthcare providers improve surgical preparedness and medical device makers to conduct testing and train medical professionals on new devices. BoneMatrix™ material with the enhanced software capabilities extends those benefits to orthopedic applications.
“We believe that better preparation leads to better clinical outcomes,” said Vice President Osnat Philipp, who leads the global healthcare team at Stratasys. “The mechanical properties of bone are so fundamental to the ability of our skeletons to support movement, provide protection for our vital organs and ultimately affect our quality of life. Being able to 3D print models that are biomechanically accurate and unique to each patient is critical to that preparation.”
Despite the high demand for bone models, traditional model options have serious shortcomings. The medical industry has traditionally used human bone from cadavers, or legacy 3D printing solutions, all of which have proven inadequate. Human bone is expensive, difficult to obtain, and hard to acquire with the precise pathology characteristics needed, such as with tumors or reflecting different ages. Off-the-shelf manufactured bone models also lack those patient-specific characteristics, and other traditional 3D printing solutions are biomechanically unrealistic. In contrast, whether inserting a screw or drilling or sawing a bone, medical professionals can expect haptic feedback from Digital Anatomy models that is very realistic, and each model can be created from an actual patient scan.
3D-printed skull and spine models for physician training workshops allow doctors to practice cutting and drilling bones, said a medical director at a children’s hospital in Florida. Her focus has been on using state-of-the-art simulation to transform pediatric training and education. “The opportunities seem endless to me because doctors can ‘operate before they operate,’” she said. “It’s going to decrease surgical time, it’s going to decrease morbidity and mortality, and help us decrease anesthesia time, which is better for brain development.”
While the 3D printer itself is cutting-edge technology, it’s the Digital Anatomy software that unlocks its power. More than 100 sophisticated presets have been developed and refined through years of expert testing, in partnership with top academic medical centers and hospitals around the world. For example, intervertebral discs can be printed normal or degenerated. The joints between vertebrae can be printed in varying degrees of stiffness. The denser structure of skull bone is differentiated from general bones. Long bones can be printed with varying amounts of marrow. Different combinations of materials are produced at a 3D voxel level to ensure the right biomechanical properties.
Researchers at the Computational Mechanics and Experimental Biomechanics Lab at Tel Aviv University conducted a clinical evaluation of the characteristics of bone models that were 3D printed on the Digital Anatomy system, specifically focusing on how accurately they replicated screw pull-out force and driving torque using cortical and cancellous screws. The 2020 study concluded that orthopedic screws pull-out force in the 3D-printed models had a similar haptic response to human cadaver bone.
A second study conducted this year by researchers at the Technion Institute of Technology’s Materials Science and Engineering Laboratory in Israel demonstrated the mechanical accuracy of 3D-printed spine models compared to cadaver spines. The study was able to demonstrate that the 3D-printed models of lumbar vertebrae accurately represented the range of motion compared to published literature on human spines.
More information on the Digital Anatomy 3D printer is available online.
Stratasys is a global leader in additive manufacturing or 3D printing technology and is the manufacturer of FDM®, PolyJet™, and stereolithography 3D printers. The company’s technologies are used to create prototypes, manufacturing tools, and production parts for industries, including aerospace, automotive, healthcare, consumer products and education. For more than 30 years, Stratasys products have helped manufacturers reduce product-development time, cost, and time-to-market, as well as reduce or eliminate tooling costs and improve product quality. The Stratasys 3D printing ecosystem of solutions and expertise includes 3D printers, materials, software, expert services, and on-demand parts production. Online at: www.stratasys.com.
To learn more about Stratasys, visit www.stratasys.com, the Stratasys blog, Twitter, LinkedIn, or Facebook. Stratasys reserves the right to utilize any of the foregoing social media platforms, including the company's websites, to share material, non-public information pursuant to the SEC's Regulation FD. To the extent necessary and mandated by applicable law, Stratasys will also include such information in its public disclosure filings.
Stratasys, PolyJet Technology, Digital Anatomy, BoneMatrix, GelMatrix, and TissueMatrix are trademarks of Stratasys Ltd. and/or its affiliates. All other trademarks are the property of their respective owners, and Stratasys assumes no responsibility with regard to the selection, performance, or use of these non-Stratasys products.
Attention Editors, if you publish reader-contact information, please use:
- USA +800-801-6491
- Europe/Middle East/Africa +49-7229-7772-0
- Asia Pacific +852 3944-8888
View source version on businesswire.com: https://www.businesswire.com/news/home/20201202005096/en/
Contact:
Media Contacts
Stratasys Corporate & North America
Aaron Pearson
Aaron.pearson@stratasys.com
+1 612-716-9228
Investor Relations
Yonah Lloyd
Yonah.lloyd@stratasys.com
+972-74-745-4919
Europe, Middle East, and Africa
Jonathan Wake / Miguel Afonso, Incus Media
stratasys@incus-media.com
+44 1737 215200
Brazil, Central America and South America
Erica.massini@stratasys.com
+55 (11) 2626-9229
Asia Pacific and Japan
Alice Chiu
alice.chiu@stratasys.com
+852-9189-7273