The new color-matching system enables the digital manufacturer to mold plastic parts in nearly any color within days
MINNEAPOLIS — (BUSINESS WIRE) — June 11, 2019 — Digital manufacturing leader, Protolabs (NYSE: PRLB) has introduced an all-new color-matching system into its plastic injection molding service. PolyOne’s PINPOINT™ Express Color and Dosing System, featuring 3M precision dispensing and dosing technologies, allows Protolabs to develop custom colors on site, drastically reducing the time it takes to mold short-run plastic parts in precise colors.
This press release features multimedia. View the full release here: https://www.businesswire.com/news/home/20190611005171/en/
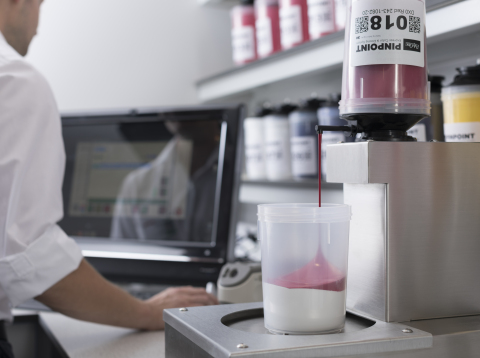
Protolabs now offers customers on site custom color matching capabilities through its adoption of PolyOne's and 3M's revolutionary PINPOINT™ Express Color and Dosing System. This capability significantly reduces the time it takes to mold short-run plastic parts in precise colors. (Photo: Business Wire)
When a part design is ready, customers can specify which Pantone number they require or simply provide a sample part that can be scanned and color matched. Once a material is selected from 13 available resin combinations, PolyOne’s PINPOINT system creates a liquid formula that is dispensed and mixed before moving to the injection molding press. The material is then fed through the doser and injection molded. The result is parts—in custom colors—in customers’ hands within days versus weeks as it traditionally takes.
“These new color-matching capabilities are a huge leap for the manufacturing industry, one stacked with benefits for our customers who are developing highly tailored products,” said Joel Matthews, global product manager at Protolabs. “With development cycles shrinking to meet the market demand for increased customization, this is yet another tool to help our customers accelerate product launches and streamline supply chains.”
Protolabs, which specializes in on-demand manufacturing, has also recently added new injection molding capabilities to further its position as a single-source supplier from prototyping to production. Along with custom color matching it has launched numerous secondary processes and finishing options to support true end-to-end manufacturing. These include pad printing and laser engraving, threaded inserts, mold texturing for Mold-Tech finishes, and part assembly.
“All of these new capabilities are things that our customers have wanted for a while, so we’re excited to finally be able to offer it to them—while still delivering finished parts at industry-leading speeds,” said Matthews.
Customers seem to agree.
“Speed and flexibility—being able to deploy different manufacturing options—and a commitment to customer service, are the main reasons we use Protolabs,” explained Andy Homyk, senior engineer at HemoSonics, a medtech firm that incorporated secondary processes to launch its new medical device in a fraction of the time traditional manufacturing would have taken.
About Protolabs
Protolabs is the world’s fastest digital manufacturing source for rapid prototyping and on-demand production. The technology-enabled company produces custom parts and assemblies in as fast as 1 day with automated 3D printing, CNC machining, sheet metal fabrication, and injection molding processes. Its digital approach to manufacturing enables accelerated time to market, reduces development and production costs, and minimizes risk throughout the product life cycle. Visit protolabs.com for more information.
View source version on businesswire.com: https://www.businesswire.com/news/home/20190611005171/en/
Contact:
Alex Cardenas
Highwire for Protolabs
650-218-8576
Sarah Ekenberg
Marketing Manager, PR & Media, Protolabs
763-479-7560